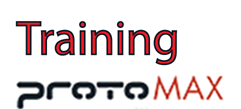
________________________________________
Nozzle Clogging: Causes and Prevention
Listed below are some of the most common causes and preventive measures for a clogged nozzle.

Use the stand-off tool provided with your machine to set the appropriate stand-off distance. See Position the Nozzle for Cutting, Set the Nozzle Stand-off. Warped or wavy material can cause the stand-off to vary throughout the cutting process. Performing a dry-run prior to cutting the part to identify the high spot on the part, and then setting the stand-off at that point. It will prevent the mixing tube from hitting the part during the cutting process.

Ensure material is properly secure on all sides. This is especially important when cutting thin and or lightweight material such as composites or plastics, as they can be pushed up by the turbulence created by the jet stream up against the mixing tube. In some cases, heavy weights such as small blocks of thick heavy steel maybe required to weigh down the material to prevent such occurrences. When using this method, ensure that the weights will not collide with the nozzle by placing them out of the way of the tool path.

This is most likely to happen when cutting thin materials, where as one piece is cut out it floats and drifts under the nozzle. If you suspect this might happen, pause the machine after the piece is cut out and remove it from the cutting deck.

Leaving abrasive inside the nozzle assembly when finished cutting will create a clog in the nozzle mixing tube. Perform a water-only nozzle test to clear out any abrasive that remains in the nozzle assembly as part of the normal shutdown process.

Keep garnet abrasive dry. Any moisture in the garnet abrasive will cause it to clump and clog the nozzle or abrasive line. Store unused abrasive in a dry, sealed container.

Moisture in the abrasive tube will cause the garnet abrasive to clump. Before machining, blow clean, dry air through the abrasive tube to remove any moisture that would compromise the garnet abrasive flow.

It is critical that you keep your abrasive clean. Any contaminant will clog the mixing tube. Use the screen provided as part of the garnet abrasive hopper assembly to screen out debris or contaminants. Keep the lid on the garnet container and the hopper lid on the garnet abrasive hopper at all times to prevent contaminants from entering the containers.
NOTE: The super high-pressure water will not blow the debris through the system. Even a tiny piece of paper can cause a nozzle clog.

The nozzle filter seal assembly affects the flow of the water into the nozzle. If damaged, dirty, or leaking, it may cause nozzle clogs. Replace after approximately 40 hours of cutting, or as needed to ensure a quality jet stream.

The garnet abrasive hopper must be grounded properly to ensure there is no static build-up in the abrasive. Static will affect the garnet flow to the nozzle, and if not flowing enough abrasive, will result in interrupted abrasive flow causing poor cut quality.

Use only OMAX-specified garnet abrasive. The quality of the abrasive is a significant factor in the performance and reliability of the machine. Using poor quality abrasives can result in frequent nozzle clogging, and poor cutting performance.

Inspect the abrasive tube as part of normal startup procedures each day to verify the tube is in good condition. Any degradation, including wear spots, cuts, frayed or rounded ends, can compromise abrasive flow to the nozzle. Replace the abrasive tube if any damage is noted.
In the event of a nozzle clog, see Recover from a Nozzle Clog.